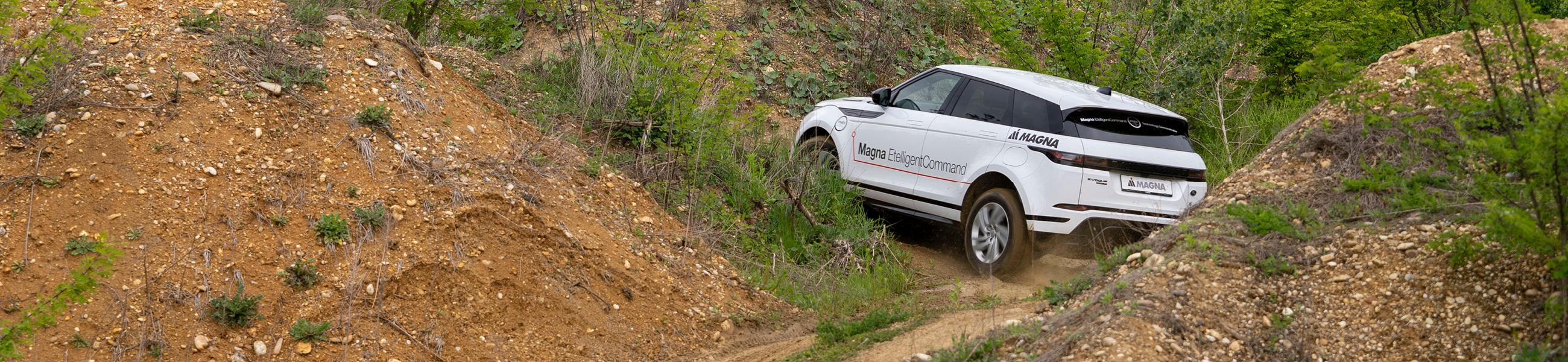
Review 2023 - DYNAMICS
Download Presentations
Please log in to download the presentations.
Address: Voestalpine-Straße 4, 4020 Linz, Austria
Franz-Josef Dorfer, Magna Powertrain
The transformation of the mobility industry has an deep impact on development methodologies and the way how we will use data over the entire life cycle of an product. How can utilize this new enabler technologies to create a smart and sustainable mobility for our future?
Dr. Daniel Tippelt, Knorr-Bremse GmbH
Magnetic track brakes are braking systems of railway vehicles independent of the wheel-rail contact, which are activated in emergency braking manoeuvres. Electromagnets installed in the bogie are lowered onto the rail and generate a magnetic attraction force between the brake and the rail. This creates a frictional force in the magnet-rail contact, which is transmitted to the bogie by the structure of the brake. To avoid high deceleration peaks, magnetic track brakes are not used until standstill of the vehicle. To reduce braking distances, especially in low wheel-rail adhesion conditions, magnetic track brakes are to remain active until standstill in the future. However, severe vibrations of a magnetic track brake were detected in vehicle tests at low velocities, leading to high mechanical loads and thus impeding this target.
The research presented focuses on identifying the self-excitation mechanisms causing these vibrations. Vehicle tests performed under realistic operating conditions are the starting point. The analysis of these tests shows periodic vibrations in an asymmetric vibration mode of the brake correlating with high magnitudes of braking forces.
To investigate the underlying self-excitation mechanism, simplified and more detailed dynamical models of a magnetic track brake are developed, which are assembled from coupled sub-models in the electrical, magnetic and mechanical domains. Model parameters required for the models are determined from vehicle tests and laboratory experiments.
By applying established methods of linear stability theory to the simplified models, two mechanisms are identified which (in combination) may cause self-excited vibrations. On the one hand, it is found that negative gradients of the coefficient of friction in the magnet-rail contact lead to negative damping terms of the system equations, resulting in self-excitation. On the other hand, an inertial coupling exists between mechanical and electromagnetic state variables, which can also cause oscillatory unstable system behaviour. This coupling is influenced both by geometric dimensions of the track brake and by the magnitude of the coefficient of friction, as well as parameters of the magnetic circuit. For systems with multiple magnets in series connection, this self-excitation mechanism is amplified for asymmetrical oscillation modes. Time-domain analyses determine the energy sources for maintaining the resulting limit cycles.
Using a more detailed multibody dynamics model, the findings obtained with the simplified models are validated and braking manoeuvres are simulated, which are compared with vehicle test data. It is shown that self-excited vibrations of magnetic track brakes are dependent on both design parameters and external influences such as accumulation of material on friction surfaces, as well as the magnet-rail contact conditions. To avoid self-excited vibrations at low velocities in the future, new designs are proposed to increase the braking capacity of rail vehicles.
Dipl.-Ing. Daniel Lichtenecker, Technical University of Munich
To keep up with the increasing demand for high-end solutions that meet a wide range of requirements in industry, it is necessary to consider novel approaches in the early stages of virtual product development. For example, computing an optimal control of flexible multibody systems is essential to perform a desired manipulation. In addition, lightweight structures require the consideration of structural optimization. This talk will focus on combining both optimization tasks in order to provide a lightweight structure regarding an optimal control problem.
Dipl.-Ing. Robert Schurmann, Volkswagen AG
For the subjective assessment of cracked axle components, complex real vehicle tests are currently being carried out. For this purpose, a crack is produced at the required location in the component to be tested and the dynamic driving behaviour is then subjectively assessed. This procedure is very time-consuming and expensive, requires the availability of prototypes and puts the test driver in a dangerous situation in the event of component failure. Consequently, the objective of this contribution is to generate a real-time capable full vehicle model with a cracked axle component that can be applied to a dynamic driving simulator. The tie rod of a four-link rear axle is selected as an exemplary component, since this component is particularly critical with regard to the driving behaviour. So far, real-time capable models with deformed axle components based on linear flexible bodies can be generated. Their influence on the dynamic behaviour of a vehicle can be tested in a dynamic driving simulator. However, for axle components with cracks, non-linearities can occur, so that a non-linear real-time capable substitute model for the cracked axle component is required.
In particular, the tie rod is loaded by tensile and compressive forces. Consequently, its substitute model consists of two rigid rods connected by a parallel circuit of a translational guide joint and a substitute stiffness in the longitudinal direction of the tie rod. The equivalent stiffness thereby models the stiffness reduction due to the crack. In the first step, a tensile and compression test is carried out experimentally and simulatively on tie rods that have cracks of different lengths in the middle of the component. The obtained force-deformation curves are used as a basis for calculating the equivalent stiffnesses related to the individual crack configurations. In the next step, a finite element (FE) semi-axle model is used to evaluate the influence of the cracked tie rod on the toe and camber angles in a stationary cornering as static load case. The tie rods with the different crack configurations are modelled as a nonlinear FE model, as a linear flexible body and via the substitute model. Above a certain crack length, the linear approach with flexible bodies leads to deviating toe and camber angles from the nonlinear FE model. In contrast, the results of the substitute model agree with those of the nonlinear FEM for all crack lengths. Finally, the vehicle dynamic properties of the different crack configurations are quantified with a steering angle ramp and a steering angle sinus sweep using a multibody full vehicle simulation. It turns out that the tie rod is quite insensitive to a crack, as significant changes in the driving dynamic characteristics only occur with a long crack. The axle model with the modelling of the cracked tie rod as a non-linear substitute model is converted into a real-time capable map model for the software CarMaker using a virtual axle kinematics test bench. The real-time capable axle model delivers comparable results to the complex non-linear MBS model, enabling the application on the dynamic driving simulator.
Dr. Wolfgang Witteveen, University of Applied Sciences Upper Austria
This paper discusses an iterative algorithm for coupling arbitrarily many dynamic subsystems (simulation and/or test bench) into an overall system. One conceivable application would be the coupling of globally distributed numerical simulations and test benches (HIL) to form an overall dynamic system. Another example is the coupling of two test benches on two different test fields to one overall system, because the monolithic overall system would be too large for one test field.
Similar to virtual iteration, this is an iterative method in which the control signals of the subsystems are modified until all cutting quantities are approximately equal. Besides the disadvantage that several runs of all involved subsystems are necessary to achieve a coupled overall system, the following advantages can be mentioned: (1) The coupling does not neglect any dynamics or nonlinearities. (2) Secrecy is guaranteed, since only transfer functions from the individual subsystems are required. (3) There is no communication between the subsystems during a run. Thus, no special requirements for data exchange are necessary. Data transfer via email is conceivable. (4) No controllers are necessary. (5) If numerical subsystems and test benches are to be coupled (HIL), then the mathematical models can be arbitrarily complex. No real-time capability is necessary.
In addition to an explanation of the method, two examples are shown. The first example is a purely numerical example with three subsystems. It is shown that the distributed simulation converges to the same solution as if a monolithic overall system is considered. In the second example, a model car is considered on a four poster test rig. The vehicle on the four poster is a multibody simulation model. Two shock absorbers are considered as hardware on the test rig. It is shown that the cutting quantities are approximately equal in a few iterations.
Dr. Gernot Jedinger-Pauschenwein, AVL List GmbH
Virtual and accurate load case definition is one challenge in modern off-road vehicle development to ensure correct dimensions and lightweight design in an early development stage. AVL have developed a methodology therefor based on vehicle multibody system simulations with MSC Adams and FTire, whereby an agricultural tractor of a serial production was chosen as test object for this research project.
For this purpose, acceleration measurements at the wheel hubs taken in the field (short wave road profiles, i.e.: cleats) have been evaluated and analyzed, and their comparison with the virtually achieved simulation results were the basis for fine adjustment of the simulation model, especially in view of accurate tire parametrization.
To proof the new methodology, a further test track has been built up in the field, acceleration signals at the wheel hubs were measured again, whereby virtual simulations were performed with the fine-tuned model parallelly. As a result, the comparison between measured and simulated signals indicated a strong correspondence, which justifies the conclusion that a virtual multibody system simulation delivers a sufficiently accurate load case definition. It also confirms the possibility to accurately fine-tune FTire parameters for large tires.
The main advantages of this methodology are that it leads to a significant cost reduction and acceleration in the development process, and it provides a good insight to the dynamic behavior of the vehicle (tractor). Furthermore, parameter optimization can be carried out cost-efficiently, too.
Three workflow examples will be presented for typical load cases with different ways of performing strength and lifetime analyses on basis of an agricultural tractor. Requirements of the model setup and parametrization will be discussed, and the boundary conditions for the test procedures on the hydro pulse system will be derived, too. Finally, the results (e.g.: damage values) achieved on the hydro pulse system will be compared with the ones derived by finite element and mechanical fatigue analysis.
First example is the Merry-Go-Round test which is a well-known tractor test procedure, and the second one is the pendulum impact test which should ensure safety for dynamic articulation of the tractor front axle. In both cases, the load case definition is performed using cutting loads obtained from rigid multibody system simulations considering no flexible structure (except tires, springs, damper, bushings, stops, etc.).
The third workflow example refers again to the Merry-Go-Round test. However, in this case two flexible components (i.e.: exhaust system and DPF) mounted to the tractor chassis body are included in the vehicle multibody system simulation, whereby the flexibility of the structures has been considered via Craig Bampton method. The load cases for the finite element and mechanical fatigue analysis are obtained from the multibody system simulation results of cutting loads and component accelerations, based on rainflow counting and statistical methods. A lifetime assessment using Femfat will be presented as result.
Otmar Gattringer, Magna Powertrain Engineering Center Steyr
Dynamic simulation using virtual roads plays an important role in the concept phase of vehicle development. Digital customer roads or proving grounds are often not available, therefore standard tracks will be used but should lead to an equivalent result.
Full vehicle simulations of a truck were performed with different roads. The target values for the assessment of the truck are known from measured road load data. The simulated roads were mixed to a test program to achieve these target values. A fatigue analysis of rear axle parts were performed to evaluate the procedure.
The resulting test program can be used in the future to assess similar vehicles in an early stage of the development.
The paper presents a comparison of methods for the fatigue life evaluation of engine housings with respect to the internal engine loads. The motivation for the comparison is that, according to current calculation methodology, low safety factors occur around the connections of the engine to the frame. This means that the connection points are not designed to be operationally stable according to numerical calculation. The safety factors are based on a quasi-static calculation methodology and an analysis with FEMFAT TransMax, which uses individual stress results from an FE analysis. The loads result from an external multibody simulation. The experimental strength tests and the evaluation of endurance vehicles show that the connection areas can be regarded as operationally stable. To verify whether the deviations are due to the quasi-static calculation approach, a calculation methodology with a dynamic approach is developed. To this end, the model was expanded to include key components of the entire vehicle to represent the dynamic behavior of the engine under internal engine excitation. The results of the new methodology, which are calculated with FEMFAT ChannelMax from modal input variables, show for the problem that more realistic safety factors are calculated with the same load signals. This can be attributed to the inertias of the masses, which lead to a changed force flow in the area of the connection points in the dynamic calculation. Based on the results of the dynamic calculation, it was investigated to consider the dynamic influence in the static non-linear analysis, which minimizes the duration of the calculation and allows the influence of non-linearities to be investigated.
Modern vehicles contain numerous subsystems for comfort, safety, digitalization, electrification and autonomous driving functions that are mounted to the body-in-white structure. These subsystems are submitted to stochastic vibrational loads induced by the road unevenness. The vibration fatigue behaviour of the subsystems and their connection to the body-in-white structure depend on a great number of influence parameters and associated uncertain scatter bands that are usually unknown and difficult to consider in the design process.
Even minor uncertainties in the characteristic properties of the mounted components can lead to significant changes in the oscillation behaviour. An inappropriate modification of the oscillation behaviour can result in a shift of the eigenmodes and natural frequencies towards a peak of the excitation and lead to resonance of the system. Consequently, the fatigue lifetime of the component or the connection to the body-in-white structure is massively reduced. In order to ensure the structural durability of the mounted components and body-in-white structure a numerical concept for consideration of uncertainties in the input parameters is created.
The methodology proposes an analyzation of the relevant natural frequency range of the system and critical hot spots with respect to the calculated damage. For the identification of the most significant influence parameters in relation to the target variables, sensitivity analyses are applied. The scattering of damage and fatigue lifetime is investigated by using a Monte-Carlo-Simulation. Finally, the reliability and robustness of the system is evaluated.
The proposed concept is illustrated by a current automotive subsystem mounted to thin plates which replicate the body-in-white structure. The implementation of the multiparameter variation is realised by the commercial optimization tool Optimus. Within the program a simulation tool chain is build up consisting of MCS Nastran for the conduction of a modal frequency response analysis and FemFat Spectral for the calculation of the damage and fatigue lifetime of the subsystem.
It was shown for the studied system that the damping, the mass and thickness of the mounted component, as well as the thicknesses of the plates have a major influence on the vibration behaviour of the system. Furthermore, a correlation between natural frequencies and calculated damage was derived. With decreasing natural frequency, the predicted damage to the system is increased. As a conclusion, it is recommended to consider a target value and limits for the natural frequencies in addition to the simulated fatigue life for mounted components submitted to vibrational loads.
A further aspect of this study is the application of super elements as a model order reduction technique. In order to save computing time and capacities the mounted components can be realised as super elements with a reduced number of relevant input parameters (mass, stiffness, damping) for implementation of the method in full-scale car simulations.
Dipl.-Ing. Markus Breitfuss, Magna Powertrain Engineering Center Steyr
The simulation-based fatigue assessment of car body structures is an essential part of modern vehicle development processes and facilitates reaching the respective durability, lightweight and cost targets. This talk provides an overview of three selected simulation processes and how they complement each other.
The first one relies on inertia relief analyses and delivers the baseline fatigue results. The second one relies on a linear dynamic simulation and enables the identification of potentially critical areas due to vibrations. However, despite detailed and fine meshed FE models one observes that both approaches lead to overestimated damage results at certain areas, mainly at spot-welded connections. Previous investigations suggest this overestimation is due to the neglected contact stresses as both methods rely on a linear model. Therefore, the third simulation process relies on a mode based dynamic contact analysis to circumvent this limitation of the other two approaches.
Throughout this talk selected results from the fatigue assessment of a car body structure are presented to point out the respective characteristics of each simulation process.
Dr. Hermann Sikora, Raiffeisen Software GmbH
In the “digital age”, leadership—in the meaning of the skill for “working on a system/business model”—is of paramount importance. Rapid technological change coming with digitalization enters all aspects of life, so businesses are forced to undertake extensive transformation processes. A strategic and pervasive positioning of information technology (IT) as business enabler and fundament of business models is of essence. Cultural business conflicts with the positioning of other operational units are unavoidable. Traditional methods of management are certainly being tested. The “digital society” needs executives with new competencies and businesses based upon fundamentally changed business cultures.
Address: Am Pöstlingberg 14, 4040 Linz, Austria
Dipl.-Ing. Tomas Gejgus, Bundeswehr University Munich
When dynamic loads act upon rubber isolators used in electric vehicles, the response of the material is highly nonlinear and can vary significantly in the region of structural resonances. For this reason, it is of interest to be capable of dynamic measurements to determine dynamic stiffness on both the sample and the component level in a relevant frequency range. In addition, the density of the industrial blend has a tremendous impact on the response in the resonance region- this was analytically shown by Lion and Johlitz in 2020 and later experimentally verified by Gejgus and Farkas in 2022. The aforementioned effect stays undetected by conventional measurement methods due to their lower frequency range. Since this dependence of the material response is strongly affected by the current temperature of the elastomer as well, further experiments, such as temperaturedependent pycnometry or thermal mechanical analysis are performed to quantify these aspects.
Moreover, further improvements of the test bench for dynamic stiffness (TBDS) introduced by Gejgus and Farkas in 2022 are presented and, with respect to the aforementioned, the influence of thermal effects during the test is observed with help of the thermographic camera. The captured impact is considered within further calculations.
The focus of this contribution then shifts to the development of the master curve – firstly, the geometrical approach of curve generation is compared with wellknown shift principles. The relevance of the free choice of the reference temperature is investigated as well. Subsequently, the master curve is approximated via the Prony series and both the raw master curve and Prony series parameters are used as the definition of viscoelastic material behaviour within two different FE simulations. To define the hyperelastic behaviour of the material,parameters of different free energy functions were optimised and the model with the best measurement approximation was chosen. Furthermore, the quasistatic experiments using digital image correlation (DIC) were conducted to investigate Poisson’s ratio of the elastomeric blend and its impact on the simulation and internal resonances of the rubber mount.
The deviations in simulation results caused by said definitions of viscoelasticity and the influence of the compressibility of the rubber compound connected to hybrid formulation are presented and discussed.
Lastly, the torque and vibration profiles during the run-up of the electronic commutated permanent magnet synchronous motor (PMSM) are measured with various boundary conditions. First, the torque profile is determined by performing the measurement with the PMSM connected to the active load unit and is further used to optimise the parameters of the motor controller. Afterwards, the measurement of structural dynamics of the system is conducted while the PMSM is mounted on an adaption using elastomeric engine mounts – the focus of this measurement is the vibration propagation from the motor to the vehicle chassis.
The results of this measurement are post-processed and the effects, such as slot locking, overvoltage of the power supply and pulse width modulation (PWM) are identified. These dramatically influence the noise-vibration-harshness behaviour (NVH) of PMSM, since the majority of the excitation energy concentrates in close proximity to said effects. Considering previous experimental investigations, one can determine the relevant excitation amplitudes for FE simulations and use them for advanced design of elastomeric engine mounts, which ensures a high level of driving comfort for the vehicle passenger.
Reinhard Helfrich, INTES GmbH
The Finite Element Analysis (FEA) of many solid structures like transmission housings, combustion engines, or brake systems have to take contact into account for stress simulation due to a prestressed state by bolting, gasket sealing, or braking pressure. Beyond stress simulation, all kinds of vibrational behaviour like eigenfrequencies and modes, up to sound radiation from the surface of the structures are very important to be calculated for prestressed structures. Due to developing low noise products, an optimization procedure has to be applied on top of stress and dynamic analysis to reduce the sound radiation while keeping stress values below certain limits.
The path to achieve sound and stress optimized products has to combine stress analysis, dynamic analysis, and shape optimization of the structural surface in one simulation process. While contact in stress analysis is a nonlinear phenomenon, vibrational analyses methods are typically linear, which requires a practical linearization of the contact state after stress analysis to continue with the dynamic analysis. The linearization will be based on the contact pressure calculated during stress analysis. In this way, stress analysis, linearization, and sound radiation analysis (e.g. in frequency domain) can be combined in one optimization loop, where the shape of the structural surface is modified to reduce sound radiation and to keep the stress values (e.g. principal stresses) below given limits. One effective method to optimize shapes is a freeform optimization using a non-parametric approach, which also allows to control the weight of the structure.
The paper will use an industrial example of a transmission housing to demonstrate the above outlined optimization procedure. Key results of stress analysis and sound radiation analysis as well as from the optimization are presented. In addition, the computation times are analysed to demonstrate the feasibility of the described process for practical applications in research and industry.
All simulations will be performed with the commercial FEA software PERMAS, which beside contact analysis also supports the linearization process and the sound radiation analysis. In addition, it also integrates optimization solvers in order to perform all simulation steps of this project with one software in one single computation.
REFERENCES
[1] Carvajal, S., Wallner, D., Helfrich, R., and Klein, M., "Excellent Brake NVH Comfort by Simulation - Use of Optimization Methods to Reduce Squeal Noise," SAE Technical Paper 2016-01-1779, 2016, doi.org/10.4271/2016-01-1779
The development of complex technical products, including application-specific electric motors, requires reducing effort and speeding up time to market to stay competitive. This paper focuses on reducing design time for highly efficient permanent magnet motors by using the simulation software
SyMSpace for optimization.
SyMSpace which stands for ‘System Model Space’, is a software environment for system simulation and optimization. It allows data management and orchestration of simulation chains. Setup of a simulation is made very easy by combining predefined simulation modules – so-called Components. For the simulation of electric machines, for instance, various stator and rotor models are available. These models can be combined to a complete multi-physics simulation chain as it is shown in Fig. 1. In addition to the electromagnetic finite element simulation (FE), also e.g. thermal simulations or rotor stress simulation can be carried out by adding further particular simulation Components.
The simulation chain in SyMSpace enables the fully automated execution of simulations. This creates a foundation for parametric multi-objective optimization. The software offers a variety of genetic or evolutionary optimization algorithms, including tailored variants that focus on reducing computation time, especially when using finite element simulations to evaluate the performance of electrical machines. To further improve efficiency, the optimization process uses surrogate models based on artificial neural networks (ANNs) to significantly reduce simulation times.
In addition to multi-physics simulation, special focus is given to the calculation of additional losses in the electrical machines. Using SyMSpace simulation software, we provide a detailed method for estimating these losses, which are a critical factor in determining the overall efficiency of the machine. The ability to accurately calculate these losses allows for more precise design optimization, resulting in improved performance and energy efficiency of the final product
Anton Plank, Magna Powertrain Engineering Center Steyr
On an example of an electric motor test rig setup, a finite element based NVH simulation process is shown. Starting with simulated excitation data in time domain, a set of frequency response analysis is set up and evaluated using MNOISE. A comparison between simulation results and measurements is shown and conclusion on the quality of the excitation data and the simulation process is given.
Dipl.-Ing. Markus Breitfuss, Magna Powertrain Engineering Center Steyr
Introduction
- Elastic structures with self-contact
- Model reduction considering nonlinear contact conditions
- MAMBA software toolchain
Exemplary car body investigation focusing on
- Contact definition
- Setting up the contact analysis
- Data export for FEMFMAT
Address: Landstraße 31, 4020 Linz, Austria